Типовые случаи применения различных степеней подготовки поверхности
На территории РФ действуют два стандарта, которые описывают степени подготовки поверхности: ГОСТ Р ИСО 8501-1-2014 и ГОСТ 9.402-2004. Наиболее удобным и подходящим для промышленной окраски считается ГОСТ Р ИСО 8501-1-2014, в соответствии с которым степень подготовки поверхности может быть выбрана произвольно, но при этом выбранная степень должна обеспечивать заданный срок службы покрытия в заданных условиях.
Давайте рассмотрим типовые случаи применения различных степеней подготовки поверхности, пользуясь определениями, которые дает нам ГОСТ Р ИСО 8501-1-2014.
Районы стыков и монтажных сварных швов – St3/Sa2,5
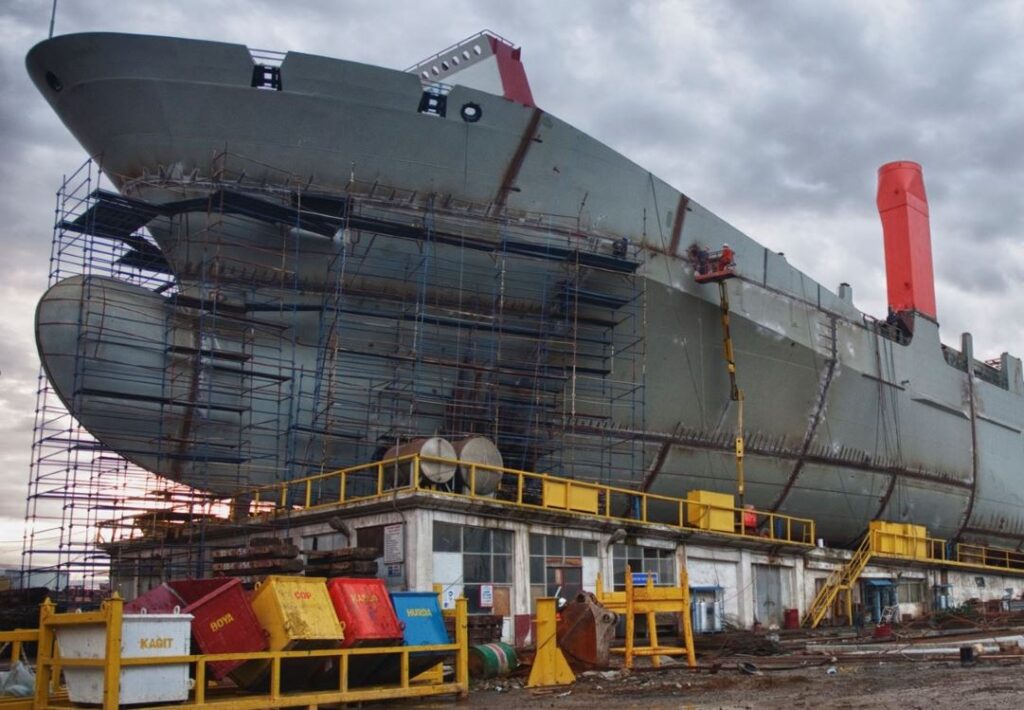
Монтажные швы на корпусе судна
Все металлоконструкции изготавливаются на заводах, после чего поступают на монтажную площадку, на которой осуществляется их монтаж в проектное положение. Аналогичная ситуация имеет место и в судостроении: сборочные цеха изготавливают секции, которые далее доставляются в стапельный цех, где секции собирают в блоки и мегаблоки. Во всех случаях после сборки металлоконструкций и секций образуются монтажные зоны и сварные швы, которые необходимо окрашивать. Обычно это вертикальные или горизонтальные участки поверхности шириной не более одного метра с небольшой общей площадью.
При строительстве новых объектов для подготовки поверхности обычно применяется степень Sa2,5, которая представляет собой прекрасный компромисс между скоростью выполнения работ, качеством покрытия и стоимостью работ. Работы выполняются в крытых цехах, при благоприятных климатических условиях, при наличии всего необходимого оборудования и эффективной организации технологического цикла.
Но как быть на монтажной площадке, где необходимо подготовить под окраску небольшую площадь, при этом условия проведения работ далеки от идеальных?
Выбирают, как правило, из двух вариантов: абразивная струйная очистка (Sa2,5) или механическая очистка (St3), при этом на практике применяется как первый, так и второй вариант.
С точки зрения срока службы покрытия выбор в пользу Sa2,5 очевиден. Кроме того, абразивная очистка дает более высокую продуктивность при выполнении работ. Но существуют и недостатки такого решения, связанные с практической стороной:
– доставка на объект оборудования для абразивной очистки, которое будет использоваться с простоями;
– возможность повреждения ранее нанесенного прилегающего покрытия абразивом;
– работы по абразивной струйной очистке невозможно выполнять вблизи от других работ из соображений безопасности. Чтобы абразив и пыль не разлетались по сторонам, требуется сооружение укрытий, вследствие чего возникает дополнительная трудоемкость и затраты;
– для производительной работы абразивоструйного оборудования необходима его установка в определенных местах и на определенной высоте;
– риск недопустимого попадания абразива на различные поверхности, в водоемы и т.п.
С учетом того, что на большинстве проектов срок службы покрытия является определяющим фактором, степень подготовки поверхности Sa2,5 имеет большее распространение для очистки монтажных зон и сварных швов.
Если ваш выбор все-таки падет на St3, то в качестве грунта рекомендуется использовать покрытия, допускающие нанесение на механически подготовленную поверхность, например, поверхностно-толерантные покрытия.
Поврежденные места на окрашенных поверхностях – St3
Как бы вы ни планировали технологию производства работ, предотвратить повреждения окрашенной поверхности на практике не удается практически никогда. Этот факт не отменяет то, что работы по окраске следует тщательно планировать, и приступать к окраске нужно только после того, как закончены все сборочно-сварочные и монтажные работы. Но даже в этом случае возможны небольшие локальные механические повреждения поверхности.
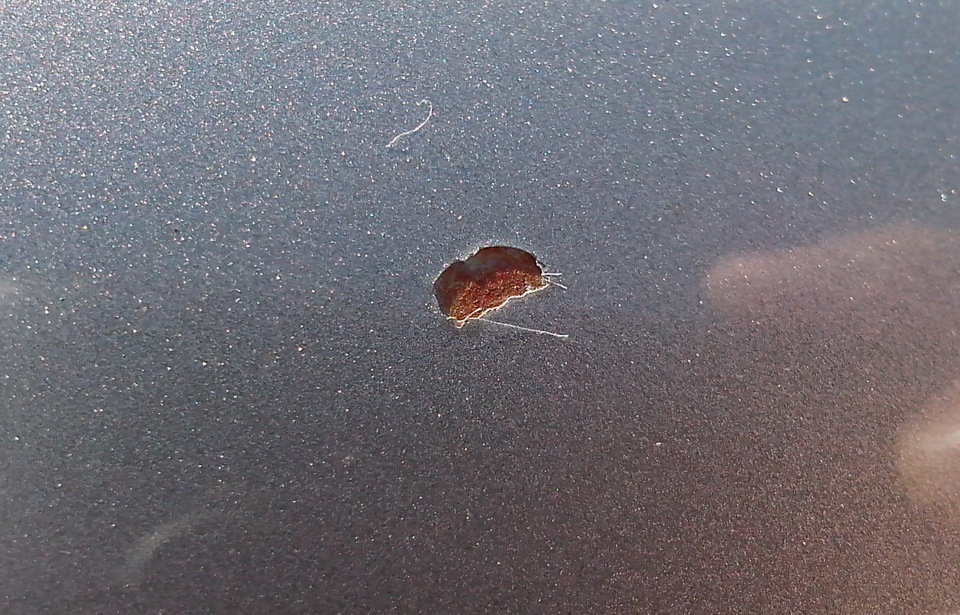
Давайте представим ситуацию, когда поверхность полностью окрашена по штатной схеме, но внезапно выяснилось, что необходимо дополнительно приварить небольшую деталь. Или потребовалась регулировка оборудования, установленного на окрашенной поверхности (частая ситуация в судостроении), и монтажники, выполняя свои работы, оставили после себя несколько сколов на покрытии. Как быть в такой ситуации?
Несмотря на то, что ко всей поверхности перед окраской была применена степень Sa2,5, для восстановления покрытия на небольших локальных участках целесообразно применять степень St3. Почему не стоит рассматривать абразивную очистку? Общее правило гласит, что для малой цели не нужно применять большие средства, но что еще более важно, это вероятность повреждения абразивом ранее нанесенного покрытия, избежать которого не удастся. Важно понимать еще и то, что почти для всех условий эксплуатации такого решения будет достаточно (при условии, что применяются покрытия, допускающие нанесение на механически подготовленную поверхность), редким исключением является лишь эксплуатация покрытия в контакте с очень агрессивными химическими веществами, но к таким покрытиям нужно относиться с особой осторожностью, не допуская их повреждения. Если же все-таки повреждение произошло, то, возможно, имеет смысл рассмотреть вакуумную абразивную очистку (мобильные абразивоструйные аппараты ранцевого или другого типа), которая отличается очень низкой производительностью, но полностью исключает повреждение смежных поверхностей разлетающимся абразивом.
Минимальную шероховатость поверхности после механической подготовки до степени St3 можно обеспечить путем ее обработки грубой наждачной бумагой – это улучшит адгезию грунта к поверхности.
Часто возникает вопрос – а при какой площади поврежденной поверхности допускается степень St3? Точного и однозначного ответа на этот вопрос нет, но давайте отметим, что ответ будет зависеть от таких факторов, как допустимость степени St3 для применяемого покрытия, фактической площади повреждения (окраски), условий эксплуатации покрытия и срока службы. В сомнительных случаях лучше обратиться за ответом к производителю покрытия.
Работы по ремонту лакокрасочных покрытий – Sa2/Sa2,5
В данном разделе под ремонтом мы будем понимать плановые ремонтные работы, когда с заданной периодичностью окрашенные конструкции осматриваются, определяется процент разрушения антикоррозионной системы, после чего приступают к удалению участков разрушенного покрытия и нанесению нового покрытия.
Отличие конструкций, бывших в эксплуатации, от новых конструкций состоит в том, что на бывшей в эксплуатации стали может присутствовать питтинг. Кроме того, участки поверхности с разрушившимся защитным покрытием, находившиеся без защиты в среде эксплуатации в течение некоторого времени, могут иметь другой поверхностный химический состав, в результате чего достижение степени Sa2,5 на таких участках будет невозможно.
Поэтому в зависимости от состояния поверхности при выполнении ремонтных работ выбирают степень ее подготовки – Sa2 или Sa2,5. Нередко выбор останавливается на Sa2, что особенно характерно для поверхностей, бывших в длительной эксплуатации в агрессивных средах. Пример: доковые ремонты судов, на которых практически невозможно добиться степени Sa2,5, но что не менее важно – это отсутствие необходимости добиваться этой степени очистки в доке, поскольку практика показывает, что подготовка поверхности до Sa2 является вполне достаточной для междокового (межремонтного) периода 3-5 лет.

При этом выбирая такую степень подготовки поверхности, заказчик экономит значительные денежные средства, так как разница в стоимости между Sa2 и Sa2,5 очень существенна. В целом, ремонтное решение, состоящее из подготовки поверхности до степени Sa2, поверхностно-толерантного грунта и остальной системы многократно доказало свою эффективность в различных эксплуатационных средах.
Планируя защиту от коррозии поверхностей с участками питтинга, следует помнить о необходимости увеличивать толщину в тех местах, где питтинг был наиболее интенсивным. Делается это нанесением дополнительного полосового слоя или за счет увеличения толщины основного слоя. Задача: увеличить толщину на пиках питтинговых участков, тем самым обеспечив надежную антикоррозионную защиту.
Труднодоступные места – St2
Сразу оговоримся, что труднодоступных мест нужно избегать. В силу своей трудной доступности на этих участках поверхности невозможно обеспечить надежную антикоррозионную защиту, что приводит к тому, что коррозия, как правило, начинается именно в таких местах.
Сделать так, чтобы конструкция не имела недоступных и труднодоступных мест – это задача проектанта. Если же все-таки случилось так, что какие-то участки конструкции остались труднодоступными, то имеет смысл попытаться заварить или заглушить их (иногда – зашпатлевать), исключив таким образом потребность в антикоррозионной защите этих участков. Оставлять участки поверхности, трудно доступные для надлежащей защиты от коррозии, допустимо только в средах с умеренной агрессивностью, в остальных случаях труднодоступные места должны быть устранены.
В крайнем случае, если перечисленные выше варианты не сработали, придется думать о том, как обеспечить защиту труднодоступных мест. Но эти места на то и труднодоступные, что сделать с ними что-либо не так-то просто. Поэтому в таких случаях обычно ставится минимальная задача – удалить с поверхности все то, что непосредственно мешает созданию адгезии. Речь о сколько-нибудь качественной подготовке поверхности не идет, поэтому ограничиваются максимумом из того, что доступно – как правило, это подготовка до степени St2. Встречаются ситуации, когда для труднодоступных мест назначается степень St3, что технически некорректно, так как для достижения этой степени требуется обработка механизированным инструментом, для которого нужен нормальный доступ к обрабатываемой поверхности. Подготовка «по-настоящему» труднодоступных мест обычно бывает возможна только с помощью ручного инструмента: щетки, наждачка, скребки и т.п.
Очистка труднодоступных мест до степени St2 и нанесение поверхностно-толерантного покрытия может обеспечить относительно неплохой срок службы защитной системы.
Ремонт покрытия на действующем предприятии – Wa2
Особенность проведения работ на действующем предприятии состоит в том, что необходимо соблюдать высокие требования в части безопасности. В частности, применительно к выполнению подготовительно-окрасочных работ, запрещено выполнять технологические операции с образованием искр и пыли, к которым относятся в том числе абразивная струйная и механизированная очистка. Соответственно, остается гидроструйная подготовка поверхности, которая имеет как свои плюсы, так и минусы, однако можно с уверенностью сказать, что в условиях действующего предприятия этот способ подготовки поверхности зарекомендовал себя как вполне надежное решение, особенно с учетом того, что ремонт покрытия на действующем производстве не подразумевает длительного срока службы покрытия, достаточно лишь обеспечить работу покрытия в течение межремонтного интервала.
Рекомендуемая степень подготовки поверхности при выполнении ремонта покрытия на действующем предприятии – Wa2 (ISO 8501-4: 2006). Обязательно применение поверхностно-толерантного грунта, поскольку в результате выполнения гидроструйной очистки на поверхности стали появляется ржавчина.
Более подробно о гидроструйной очистке читайте в нашей статье.
Поверхности с нанесенным шоппраймером – свипинг и St3/Sa2,5
Шоппраймер предназначен для временной защиты стали до момента нанесения основной антикоррозионной системы. Этот промежуток времени (между нанесением шоппраймера и основной системы) может быть большим и в зависимости от условий, в которых находился шоппраймер, может потребоваться дополнительная подготовка поверхности.
Подготовку поверхностей с ранее нанесенным шоппраймером перед нанесением основной системы можно условно разделить на три этапа:
1) подготовка участков с вновь установленными (приваренными) деталями;
2) подготовка участков с разрушенным шоппраймером (коррозия, локальные отслоения и т.п.);
3) подготовка поверхности неповрежденного шоппраймера, на которой обычно присутствуют различные загрязнения (жировые загрязнения, грязь, посторонние частицы и т.п.).
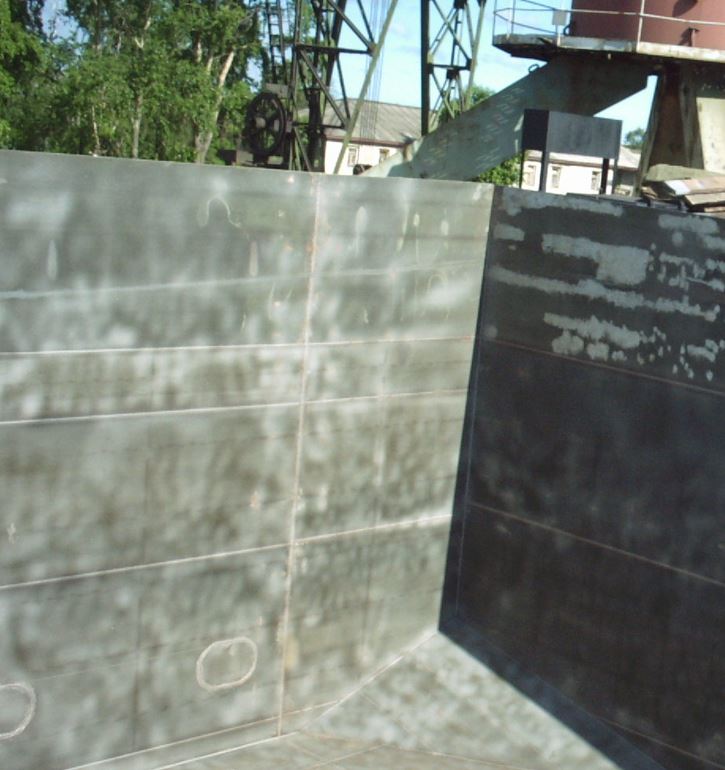
Подготовку поверхности по п.1 и п.2 обычно выполняют абразивным струйным методом до степени Sa2,5. Такой вариант часто применяется в судостроении, где площади обрабатываемых поверхностей почти всегда оказываются значительными из-за насыщенности конструкции и длительного срока хранения шоппраймера. При выборе такого способа подготовки целесообразно выполнить свипинг поверхностей с нанесенным шоппраймером – это позволяет быстро и эффективно удалить все поверхностные загрязнения.
Если же по каким-либо причинам абразивная струйная подготовка применяться не будет, то работы по п.1 и п.2 выполняются до степени St3, а по п.3 выполняется ручная и механизированная очистка неповрежденного шоппраймера.